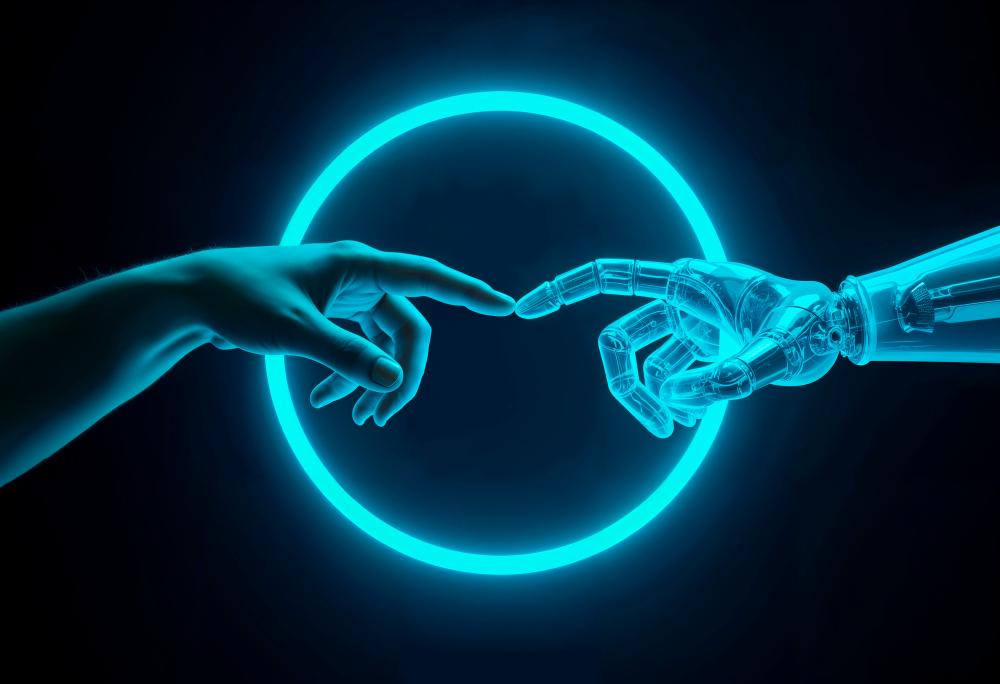
Bayangkan jika sebuah mesin, pabrik, atau bahkan seluruh jalur produksi memiliki “kembaran digital”—model virtual yang selalu selaras dengan kondisi fisik aslinya secara real-time. Konsep futuristik ini kini menjadi kenyataan dengan hadirnya Digital Twin: representasi digital dari entitas fisik yang mampu mereplikasi perilaku, menganalisis performa, dan memprediksi hasil masa depan.
Digital Twin bukan sekadar visualisasi tiga dimensi. Ia menggabungkan data sensor IoT, pembelajaran mesin, dan sistem informasi industri untuk menciptakan lingkungan simulasi yang hidup. Dengan pendekatan ini, manajer produksi bisa mengamati performa mesin secara real-time, menguji skenario “what-if” sebelum keputusan diambil, dan mendeteksi potensi kegagalan bahkan sebelum gejala fisiknya muncul.
Studi dari Journal of Manufacturing Science and Engineering (2023) mencatat bahwa implementasi Digital Twin dapat meningkatkan efisiensi operasional hingga 30% dan mengurangi downtime hingga 45% dalam lingkungan produksi berbasis data.
Salah satu contoh paling mencolok berasal dari pabrik jet engine milik Rolls-Royce. Setiap mesin yang mereka produksi memiliki Digital Twin yang memantau performa selama siklus hidupnya. Data dari sensor di lapangan dikirim ke kembaran digital yang digunakan untuk simulasi perawatan prediktif dan optimasi bahan bakar. Hasilnya, efisiensi meningkat, downtime berkurang, dan layanan purna jual menjadi lebih proaktif.
Di Indonesia, PT Pupuk Kalimantan Timur mulai menjajaki Digital Twin untuk monitoring proses reaktor dan distribusi amonia. Mereka bekerja sama dengan Siemens untuk membuat model digital yang mampu memvisualisasikan parameter proses dan memperkirakan kebutuhan perawatan, sehingga proses produksi pupuk menjadi lebih andal dan efisien.
Digital Twin juga menjadi tulang punggung dalam konsep smart factory. Sistem ini tidak hanya memetakan komponen fisik, tetapi juga proses bisnis dan logistik yang terkait. Dengan integrasi antara ERP, SCADA, dan platform Digital Twin, perusahaan bisa menyusun strategi produksi berbasis data aktual dan prediksi tren masa depan—sebuah lompatan besar dari sistem legacy yang reaktif.
Namun, tantangan tetap ada. Membangun Digital Twin membutuhkan data berkualitas tinggi, arsitektur sistem informasi yang solid, serta integrasi antarsistem yang kompleks. Oleh karena itu, pendekatan bertahap dan kolaboratif, melibatkan tim data science, IT, dan operasional menjadi sangat penting dalam implementasinya.
Di tengah tekanan global untuk efisiensi, transparansi, dan keberlanjutan, Digital Twin menawarkan jalan baru. Ia bukan hanya teknologi, melainkan cara berpikir ulang tentang bagaimana kita merancang, mengelola, dan menyempurnakan proses produksi. Sebuah kembaran yang bukan sekadar tiruan, tetapi mitra strategis di era manufaktur cerdas.
Referensi Ilmiah dan Industri
- Journal of Manufacturing Science and Engineering. (2023). Impact of Digital Twin on Industrial Production Efficiency.
- Siemens Digital Industries. (2023). Digital Twin in the Process Industry: From Vision to Reality.
- Rolls-Royce. (2022). How Digital Twins Power the Future of Jet Engine Management.
- McKinsey Digital. (2024). Reimagining Operations with Digital Twins in Industry 4.0.
- PT Pupuk Kaltim & Siemens Indonesia. (2023). Case Study: Digital Twin Implementation in Fertilizer Manufacturing.