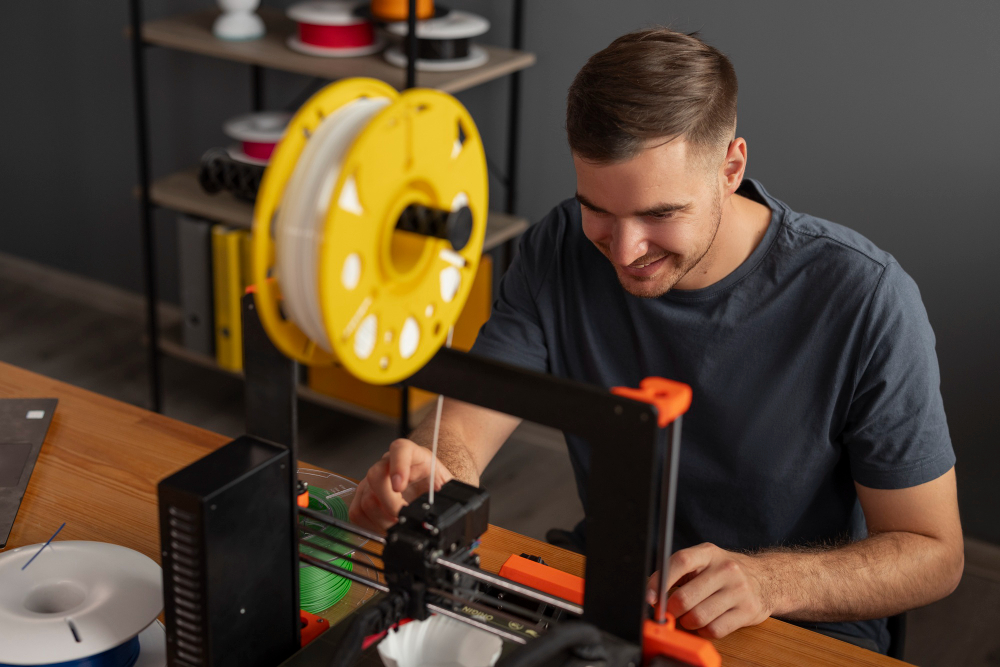
Dalam lanskap industri manufaktur modern, efisiensi operasional menjadi penentu utama daya saing. Salah satu pendekatan strategis yang kini banyak diadopsi adalah predictive maintenance—pemeliharaan prediktif berbasis data—dengan memanfaatkan kecerdasan buatan (AI), machine learning, dan Internet of Things (IoT). Teknologi ini memungkinkan deteksi dini terhadap potensi kerusakan mesin, sehingga dapat dilakukan perawatan sebelum kegagalan terjadi.
Predictive maintenance memanfaatkan data sensor yang dikumpulkan secara real-time untuk menganalisis kondisi mesin dan memprediksi kemungkinan kerusakan. AI dan machine learning digunakan untuk mengenali pola perilaku mesin normal dan mendeteksi anomali yang berpotensi menimbulkan gangguan. Menurut Lee et al. (2014), pendekatan ini dapat mengurangi biaya perawatan hingga 30% dan downtime hingga 50% dibandingkan dengan pemeliharaan tradisional.
IoT menyediakan infrastruktur penting untuk menghubungkan mesin-mesin industri dengan sistem digital. Sensor-sensor yang terpasang pada mesin mampu mengirimkan data seperti suhu, getaran, tekanan, dan arus listrik secara real-time. Data ini menjadi input utama bagi algoritma machine learning untuk melakukan analisis prediktif. Menurut Ahmad et al. (2018), integrasi IoT dalam predictive maintenance meningkatkan akurasi prediksi dan efektivitas keputusan pemeliharaan.
Beberapa algoritma yang umum digunakan dalam predictive maintenance antara lain Support Vector Machine (SVM), Random Forest, dan Recurrent Neural Network (RNN). Algoritma ini dilatih menggunakan data historis kerusakan mesin untuk mengidentifikasi pola yang mendahului kegagalan. Berdasarkan studi oleh Zhang et al. (2019), penggunaan RNN memungkinkan model menangkap dinamika temporal dari sinyal sensor, sehingga prediksi menjadi lebih akurat.
Siemens telah mengimplementasikan sistem AI dan IoT dalam fasilitas produksinya untuk memantau kondisi turbin dan motor listrik. Melalui platform MindSphere, Siemens mampu mendeteksi anomali sejak dini dan menjadwalkan perawatan secara otomatis. Hasilnya, perusahaan berhasil menurunkan waktu henti produksi hingga 45% dan menghemat biaya pemeliharaan jutaan dolar per tahun (Siemens, 2020).
Meski potensinya besar, implementasi AI dalam predictive maintenance menghadapi tantangan seperti kualitas data, integrasi sistem lama, serta kebutuhan akan keahlian teknis. Menurut Carvalho et al. (2019), solusi terbaik mencakup peningkatan interoperabilitas perangkat, pelatihan SDM, dan pengembangan model hybrid yang memadukan data sensor dan pengetahuan domain.
AI dan IoT membuka jalan baru dalam efisiensi pemeliharaan industri. Predictive maintenance bukan sekadar tren, tetapi kebutuhan strategis dalam menghadapi kompetisi global. Studi kasus seperti Siemens menunjukkan bahwa dengan penerapan yang tepat, perusahaan dapat mengurangi downtime, memangkas biaya, dan memperpanjang umur aset produksi.
Referensi:
- Lee, J., Bagheri, B., & Kao, H. A. (2014). A Cyber-Physical Systems architecture for industry 4.0-based manufacturing systems. Manufacturing Letters, 3, 18–23.
- Ahmad, R., Kamaruddin, S., & Nor, M. J. M. (2018). A review of predictive maintenance: Case study on production systems. Journal of Industrial and Intelligent Information, 6(1), 23–30.
- Zhang, W., Yang, D., & Wang, H. (2019). Data-driven methods for predictive maintenance of industrial equipment: A survey. IEEE Systems Journal, 13(3), 2213–2227.
- Siemens AG. (2020). Predictive maintenance with MindSphere: Real-time insights into machine health. Siemens White Paper.
- Carvalho, T. P., et al. (2019). A systematic literature review of machine learning methods applied to predictive maintenance. Computers & Industrial Engineering, 137, 106024.